SynTouch, spun off from USC research, is using robot touch to improve everything from cars to toilet paper to online shopping.
No longer are products just “soft” — they are Toccare data consisting of 15 different dimensions of measurable physical qualities such as “macrotexture coarseness,” “sliding resistance” and “thermal cooling.” SynTouch calls these Toccare Haptics Profiles, which define numerically how any material feels to the touch. Clip Nail Machine

Have you ever wished your scratchy old wool sweater was softer but still heavy and warm? Wanted your running shoes to be lighter but still cushion your feet with every step? What if your car’s interior dripped with the luxury of the finest Italian leather without you having to compromise your budget? What if the feeling of every product you bought was dynamically designed to feel the best it possibly could?
The answer, according to SynTouch, a tech startup spun out of the USC Viterbi School of Engineering, may be robot touch — the ability for machines to synthesize and quantify the human sense of touch.
Take Velcro Companies, for example.
Velcro was seeking help to improve their diaper fastener technology in an innovative way. Diaper fasteners need to be soft to the touch but appear strong and resilient, and the research SynTouch conducted — assessing both visual and tactile attributes of diaper fasteners — provided the feedback Velcro needed for product innovation.
Velcro is not the only brand using SynTouch’s technology to stay ahead of the curve; the brand is joined by a handful of other Fortune 500 companies such as Hanes, Volkswagen, Microsoft, Google, L’Oréal, Ford and Adidas to name just a few. This impressive list of clients spans across multiple industries, including nonwoven fabrics and products, apparel, automotive interiors and exteriors, cosmetics, and consumer electronics, all industries that provide consumer products and could benefit from improving the feel of their commodities.
So, what service is SynTouch providing for these companies? Why would Volkswagen be interested in the services of a small technology company that started as research in Professor Gerald Loeb’s Medical Device Development Facility?
SynTouch advertises its Toccare® Haptics Measurement System as objective evaluators of how consumer goods feel to the touch, how to improve that feeling, and how to consistently reproduce that feeling through quality control.
The tactile sensors developed in Dr. Loeb’s lab at USC allow the Toccare instrument developed by SynTouch to mimic and quantify how human fingers sense and move and are capable of precisely quantifying the force, vibration, and thermal elements of all materials.
No longer are products just “soft” — they are Toccare data consisting of 15 different dimensions of measurable physical qualities such as “macrotexture coarseness,” “sliding resistance” and “thermal cooling.” SynTouch calls these Toccare Haptics Profiles, which define numerically how any material feels to the touch.
For the Toccare instrument, the sense of touch is recorded not as electrical signals communicated to the brain, but as a set of numbers that the machines have no preference for or against.
Once the instruments data are translated to human perception, the possibilities of what can be done with the data are plentiful.
Companies can compare their products to benchmarks, prototypes and competitors’ materials, or better understand what material properties result in descriptors like “rough” and “soft” and what variables they can change to achieve the most desirable effect. The technology has the potential to predict the feel of materials before they are manufactured, or throughout the design and production process. Toccare data also inform how changes in product cost, sustainability and performance will affect how they feel. So just as Velcro used SynTouch technology to evaluate consumers desires for feel and performance of diapers, a global manufacturer of performance apparel is using SynTouch to develop new fabrics that are breathable and sweat wicking, while still being insulating and warm, all while still feeling soft to touch, environmentally friendly, and most importantly affordable for the consumer.
And yet 15 years ago, before SynTouch was being recognized by global brands, it was a research project in Loeb’s lab.
Loeb, who currently serves as a board member to SynTouch, developed the original prototype of SynTouch’s sensing technology with members of his lab, Matt Borzage, Ph.D. ’14, and Jeremy Fishel, Ph.D. ’12, now company advisors, using a seed grant from the Tech Futures Institute and expanding previous research the lab had been involved in with the Defense Advanced Research Projects Agency (DARPA). The team was prototyping tactile haptic sensors for use in robotic prosthetics, hoping to give robotic prosthetic hands the ability to identify and quantify the amount of force to use when handling different objects.
When humans pick up or touch something our fingers and skin can identify the object from its tactile variables and instantly determine the amount of force to use when handling the object. A robotic prosthetic, on the other hand, cannot differentiate between the necessary force to apply when picking up an egg versus a wrench, resulting in a lot of broken eggs and an increased difficulty when performing everyday tasks that non prosthetic users may take for granted.
Loeb, Borzage and Fishel, pleased with the results of their original design, sought out funding to develop a less primitive prototype. However, they were turned away by the National Institutes of Health (NIH) and National Science Foundation (NSF) because their tech was already viable and ready for commercial development.
Although hardly an issue to be told your research is too developed, they were advised that their project would be perfect if they were applying for a Small Business Innovation Research grant. The problem? They were not a small business. They were a faculty member and two graduate students sitting on haptic sensors that had the capability to mimic the physical properties and sensory capabilities of the human fingertip.
“We all got together, I think probably in the backyard of my house, and said, what about we start a company?” Loeb recounts. “And we did.”
Right from the start, the group was aware that their sensing technology had applications, not only for hand prosthetics, but also for robotics, agricultural and military use as well; so they applied for SBIR loans from multiple organizations: the NIH, the NSF, the U.S Department of Agriculture, The U.S Department of Arts and Culture and the U.S. Department of Defense. The company was awarded them all. Now, the technology originally developed in 2007 for techno sensing in prosthetic hands is revolutionizing how we can biomimetically quantify touch and commercialize it to the masses.
Although SynTouch has seemingly established itself as a hot commodity among world leaders in a plethora of industries, Loeb and his co-founders never predicted SynTouch would revolutionize product development.
“We had no idea that this field of consumer product haptics even existed,” Loeb confessed.
“We actually published a paper showing that with this device you could identify different textured materials according to your previous experience with them much better than a human,” said Loeb. “We were actually very proud of that as a piece of academic research, and within weeks we started getting calls from people at companies that make consumer products.”
Procter & Gamble, a multinational consumer goods conglomerate that specializes in hygiene products and has an annual revenue of around $80 billion, was one of the most interested companies. It’s easy to see why the company that produces Charmin Ultra Soft Toilet Paper may pay special interest into how their products feel to consumers and ways to streamline the process considering the resource heavy and imprecise process of running consumer panels to determine the desirability of a product. Because consumers are so subjective, SynTouch was able to convince companies that their technology is capable of objectively determining a product’s feel which saves time, money and noise.
SynTouch’s deviation from the prosthetic applications of its technology may seem random, but Loeb explained that the company was fortunate to pivot to consumer product testing because the prosthetics industry is not quite ready to integrate tactile sensors into the robotic prosthetics being produced.
Sensory inputs from touch produce vast amounts of tactile information that our brains interpret to make very sophisticated use of our hands, but in most cases, we still don’t understand how all the tactile information is decoded into actual control, and until we do, robotic hands have little use for tactile sensors. Even if there was a more comprehensive understanding of the neuroscience behind performing simple everyday tasks and tactile sensors could be integrated into robotic prosthetics, insurance proves a whole other issue.
“I’ve been working in neuroprosthetics for essentially all my career, and you know, insurance coverage for things like that is extremely limited.” Loeb knows from experience that any technology that adds complexity and fragility to a prosthetic and will be exposed to the hazards of everyday life will be difficult to market because of coverage issues. Loeb stays hopeful that robotic hands and industrial robots will one day be able to make use of the tactile sensors SynTouch develops, but until the underlying physiological functions are understood, robotic sensors will still rely on human interpretation and robotic prosthetics will be hindered from making it to the market.
Presently, SynTouch partitions its time between developing sensors to be used in the limited research market of prosthetics and building machines and conducting studies for consumer products. However, the company is constantly looking for new ways to apply and integrate their technology into other sectors of consumer goods.
“Another area that we’ve been looking at very vigorously is e-commerce,” Loeb said, describing a common issue people have when they buy things online like towels or sheets. “One of the biggest problems e-commerce has in those areas is that they ship things to consumers who say: ‘I don’t like how this feels,’ and ‘I couldn’t tell from the web page.’”
The company is interested in helping develop ways of encoding and comparing information to consumers online so they don’t make the mistakes of ordering materials they don’t desire and can avoid returning expensive goods. For the consumer, this would mean recommended products based on how the customer enjoyed previous products of the same materials. An algorithm that knows you enjoy softer sheets but won’t pay above a certain price for them, also that you care about the environment, and you only buy products that are sourced from recycled materials, but only if they can also keep you warm in the winter. If Toccare data can be used to create standards of measurement for material quality and feel, then all the nuances of a customer’s desires can be scaled and ranked across multiple materials and products.
You can imagine a website saying: “You liked these towels that are a ‘7’ for softness, according to Toccare haptic sensors — these sheets scored similarly, and we think you would enjoy them.”
The goal of being able to tell a consumer on an e-commerce site that a product will feel like something they already know and enjoy requires the incorporation of Toccare technology throughout the entire supply and products chain, starting with the selection of raw materials. Another example of how Toccare sensors could be utilized in the future is throughout the development of more sustainable products, an issue becoming increasingly relevant to consumers and product suppliers.
“There’s a lot of interest in using recycled fabrics and recycled plastics to make fabrics and synthetic materials. But it’s well known that when you recycle materials their haptic properties change; and how you recycle them, and how you reconstitute them and how you mix them produces very different haptic senses.”
Loeb asserts that having objective knowledge of those materials in the supply chain can inform how to achieve the desired product.
SynTouch may not yet be an industry of its own or raking in the same revenue its clients, but the company has come a long way from its humble beginnings as an office space a few blocks off USC’s campus. Loeb is the first to admit the company is not exactly rich but also recognizes the progress SynTouch has made.
“I think the first thing about startup companies is if they’re still in business 15 years after you started them. You must call it a success.”
SynTouch’s survival since 2007 indicates there is a space for the technology, and it has potential directions to grow in. So, what should we expect from SynTouch right now?
“I really don’t know, right?” Loeb honestly answers. “You follow your business, and if you want to stay in business, you have to follow where your customers want it to go.”
Loeb also sensibly points out the natural progression of start-ups and the transitions that have occurred at SynTouch over the last six to eight years: “The business has to go from people who love the technology and love the science and want to make better things, to the people who know how to find clients, to educate them, to deal with whatever their misconceptions are, and successfully run a business.”
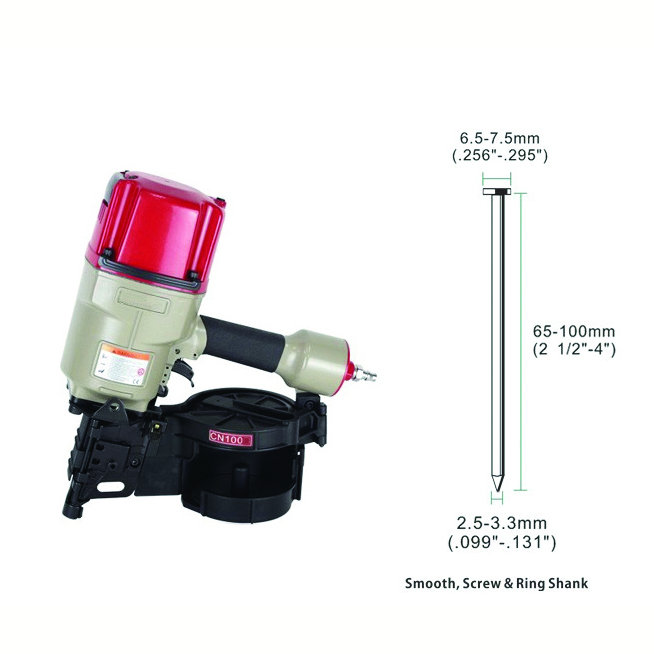
High Speed Nail Making Machine Price Last updated on January 26th, 2023