Loose-fitting powered air purifying respirators (PAPR) provide higher levels of respiratory protection compared to tight-fitting half-face respirators or disposable respirators. Photo courtesy of 3M Canada.
Safety on the shop floor should be at the forefront of every welder’s mind, especially when it comes to potential exposures to the hazardous fumes, gases, and vapours associated with welding. Shops need to begin with a holistic approach to minimizing exposure through proper industrial hygiene practices, including hazard identification, evaluation, and control. Once these are in place, shops can then focus on determining the best respiratory protection for workers. Passive Welding Helmet
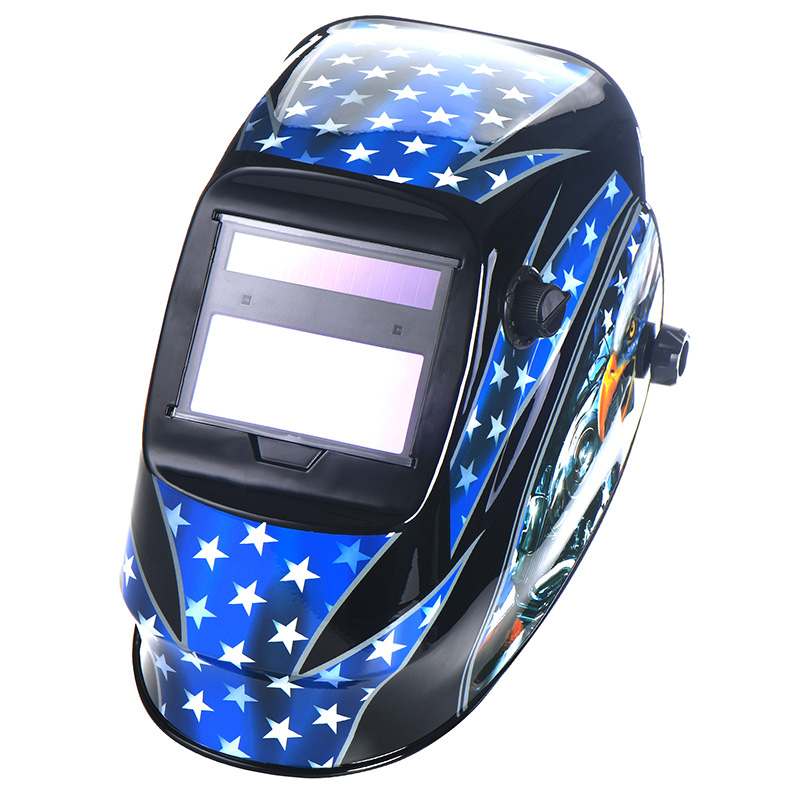
Andrew Gill, business development program manager, personal safety division, for 3M Canada, London, Ont., and Stacey Blundell, senior H&S application specialist for 3M Canada, discuss why powered air purifying respirators (PAPR) are becoming more mainstream and how they have evolved to meet today’s demanding environments.
Canadian Fabricating & Welding: What do shops need to consider when it comes to welding safety?
Stacey Blundell: Proper industrial hygiene practice requires that certain steps be taken before any shop looks at using respiratory protection. It’s not as easy as just putting on a PAPR. Employers are required to explore ways to eliminate or reduce whatever hazards workers are being exposed to and implement controls. This could include changing the way they are welding or using different materials.
Another common control measure is the addition of a proper ventilation system to capture welding fumes. Shops can also change worker techniques, add worker training, or reposition work flow to reduce exposure to the welding fumes. After a shop has exhausted all avenues, workers could still be overexposed, and that’s when they must include respiratory protection.
An assessment of workers’ exposures to airborne contaminants is first conducted. If the measured exposures are below the applicable occupational exposure limits, respiratory protection may not be required (although it should still be used as certain components of welding fume are confirmed carcinogens). However, if they are above the limits, respiratory protection is mandatory.
The use of respiratory protection in the workplace is highly regulated. The specific legislative requirements vary from province to province.
In general, the employer needs to establish a respiratory protection program based on the CSA Z94.4 standard. This standard outlines the requirements for a respiratory protection program, including its administration, roles and responsibilities, hazard assessment, respirator selection, use and care, training, fit-testing, medical surveillance, recordkeeping, and program maintenance.
CFW: What types of respiratory protection should shops be looking into?
Andrew Gill: Several levels of respiratory protection are available. A disposable or half-face tight-fitting respirator may be an appropriate option where exposures are low and is generally where a shop would start out. However, there is a trend in the industry to move to welding PAPRs.
This PAPR can be configured depending on what kind of headgear the welder needs. For example, if the welder will also be grinding, he can flip the PAPR to reveal a grinding visor underneath. Photo courtesy of 3M.
Blundell: A loose-fitting PAPR provides higher levels of respiratory protection compared to a half-face tight-fitting respirator or disposable respirator. Another benefit of this option is that it can be worn by welders with facial hair in certain situations. We are seeing more and more welders that do not shave daily or like to sport a beard. When using a disposable or reusable half-face respirator, the welder is required to be clean-shaven and undergo fit-testing, per the requirements of the CSA Z94.4 standard. A loose-fitting PAPR can accommodate a certain amount of facial hair and does not require fit-testing. These are two time-consuming requirements that can be eliminated.
Another benefit is comfort. The other two options have breathing resistance, but loose-fitting PAPRs do not. If the welder is required to wear respiratory protection for a long time, having a system that uses a fan to provide a constant flow of filtered air is much more comfortable. The constant airflow into the helmet also provides the welder with a breeze across the face and head. When the welders are in warm conditions, this can help cool them, again making them more comfortable. All of this would contribute to productivity gains and better worker conditions.
CFW: How do PAPRs interact with other PPE?
Blundell: When welding, welders may need to be wearing several types of PPE. At a minimum, they need some type of respirator and a welding helmet to protect themselves from the welding arc. Underneath the welding helmet, they also need safety glasses. In addition, they may also need a hard hat and hearing protection. Skin protection is also required because the bright light that you see when someone’s welding gives off a lot of UV light, which causes skin cancer.
So we’re talking about a minimum of five or six different types of protection needed when welding. When a welder switches over to a PAPR, all those elements of protection can be found in one piece of equipment, except for safety glasses, which are still required to be worn with PAPRs.
A PAPR headtop designed for welding can protect the eyes and face and can include an integrated hard hat. A welder can also incorporate earmuffs attached to the side or a shroud covering the front and back of the neck to protect against UV light. So using a PAPR gives a welder the versatility of having lots of protection in one system, giving better fit and more comfort.
CFW: How can the PAPR system be configured?
Gill: PAPRs generally are configured as a belt-mounted or backpack unit. From that, the system is highly customizable to meet the needs of the application. A welder can determine the headgear, visor, and lens requirements. Depending on what kind of headgear the welder needs, the system can be configured to meet those needs.
For example, does the welder need only a soft top? Or will the welder also be grinding? In that case, we can add an option that when flipped will reveal a grinding visor underneath. Has the Ministry of Labour mandated that a job site requires head protection? A PAPR can include a hard hat option in conjunction with the weld shield. The welder also has the option to choose the correct welding lens for the application, whether that’s the traditional autodarkening lens or an autodarkening option with a true-colour lens.
Versatility is really something that comes to mind with a system like this. When a welder purchases a PAPR, they are not locked into a standard configuration. For example, if a welder purchases an around-the-waist unit with particulate filter for welding fumes, with certain models, they can later add a chemical cartridge to adapt the system for exposures to certain gases and vapours. If the welder is moving into other jobs beyond welding, he or she can switch to a clear visor instead. The idea behind the PAPR system is that it offers users multiple functionalities in one unit, especially because it is a significant investment.
CFW: What sort of training and maintenance are needed for proper PAPR use?
Blundell: Training is absolutely necessary, and requirements are indicated in the CSA Z94.4 standard. In addition to that, welders need to be trained on the individual requirements of the product or PAPR being used. The products nowadays are more and more advanced. They can actually alert welders to when, for example, they need to change the particulate filter because it’s full or when they need to charge the battery. If welders haven’t been trained on the product, they may not be able to properly interpret some of the notifications.
On the helmet itself are components that need to be replaced at certain intervals. It’s a pretty big purchase, so it’s important to know how all the features work and increase the life cycle of replaceable parts. If we see welders who don’t take care of it properly, don’t maintain it properly, don’t clean it, don’t store it properly, they may not have as good as an experience with it. Shops certainly want to make sure that welders are trained in proper maintenance so the PAPR will last a very long time.
More and more in trade schools, health and safety has become much more of a priority than it has been in the past. The younger workforce is aware of the long-term effects of workplace hazards and wants to be protected. Incorporating a PAPR can also be a great worker retention tool. It’s the latest and greatest respiratory protection option available and a way for a shop to demonstrate its support for the health and safety of its workers.
Associate Editor Lindsay Luminoso can be reached at lluminoso@canadianfabweld.com.
Canadian Metalworking / Canadian Fabricating & Welding
Toronto, M1R 0A1 Canada
See More by Lindsay Luminoso
Lindsay Luminoso, associate editor, contributes to both Canadian Metalworking and Canadian Fabricating & Welding. She worked as an associate editor/web editor, at Canadian Metalworking from 2014-2016 and was most recently an associate editor at Design Engineering.
Luminoso has a bachelor of arts from Carleton University, a bachelor of education from Ottawa University, and a graduate certificate in book, magazine, and digital publishing from Centennial College.
Read more from this issue
Subscribe to Canadian Fabricating & Welding
Find Canadian Fabricating & Welding on Facebook
Find Canadian Fabricating & Welding on Twitter
Keep up to date with the latest news, events, and technology for all things metal from our pair of monthly magazines written specifically for Canadian manufacturers!
Easily access valuable industry resources now with full access to the digital edition of Canadian Metalworking.
Easily access valuable industry resources now with full access to the digital edition of Canadian Fabricating & Welding.
• The speed, precision, and repeatability of a robot • The job-to-job adaptability of a seasoned welder • Cooper™ is your “Go There, Weld That” collaborative welding solution that is packed with advanced welding capabilities to propel your welding productivity
© 2023 FMA Communications Canada, Inc. All rights reserved.

Camo Welding Helmet Not yet registered? Sign up