There are many reasons a welder might choose to work with stainless steel; the metal is corrosion-resistant, recyclable, and tougher than most metals. Stainless steel may be tricky to get a handle on at first because the welding processes for various metals are so different. When using this metal in your projects, utilize our tips and tricks for welding stainless steel for a high-quality turnout.
Because stainless steel is a heavier metal, it requires arc welding to produce a superior weld. When it comes to your tungsten rod, it matters less about what type you use, and more about ensuring the diameter of your rod is correct. The heavier the stainless steel is, the bigger the diameter of your tungsten rod needs to be. Flux Core Welding Wire

The filler wire you choose to work with plays a significant role in determining the quality of your weld. The material in the filler wire must be equal to or greater in strength than the stainless steel. The best way to find the right size is through trial and error on a practice section of your project.
This stainless steel welding trick may be hard to perfect at first. Using excessive heat will make your project look worse in the end, and turning down your amperage will not do you any better. The key to minimizing the risk of your weld blowing through is to weld with just enough amperage; typically, you should run your weld at 10 percent less than one amp per 0.001 inch. Increase your speed to travel fast enough over the metals to match the heat temperature for a better weld.
Always shield your weld from oxygen. If it’s exposed, your weld can look ugly and discolored. Back purging ensures your weld forms smoothly; use an inert gas purging system for stainless steel. Keep your gas usage within an economical range, but know that the more gas you use, the cleaner your weld will look.
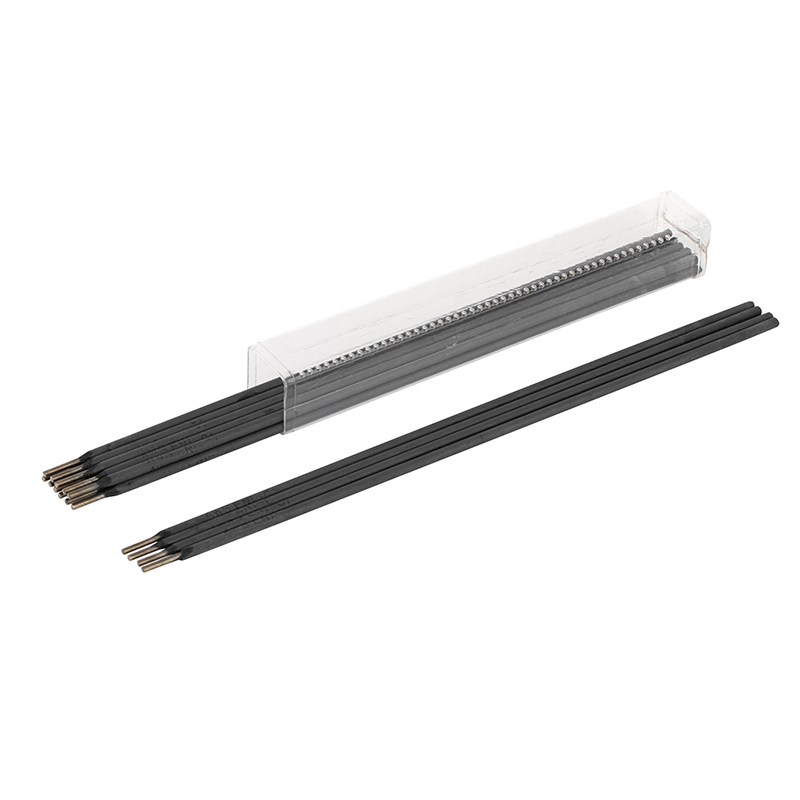
Wire Weld Now that you have a better idea about working with stainless steel, your welds will look cleaner and more uniform. The best way to sort out problems is through trial and error until you find the right balance of variables to create a weld. Practice makes perfect, and after becoming familiar with this metal, you’ll soon be making better welds.